JdeW
Enthusiast
- Messages
- 1,094
- Location
- Laarbeek The Netherlands
Chassis small update 
New heavy metal has arrived (and still I'm a big fan of the NWOBHM as well
) a repair piece of the left outer rear suspension mounting.
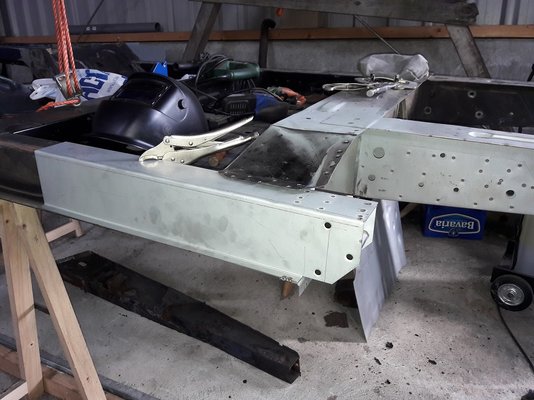
Meanwhile doing some small panel repairing...
Cutting away
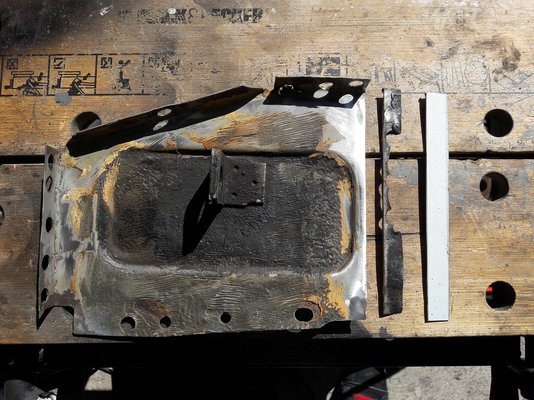
Preparing replacement steel and welding
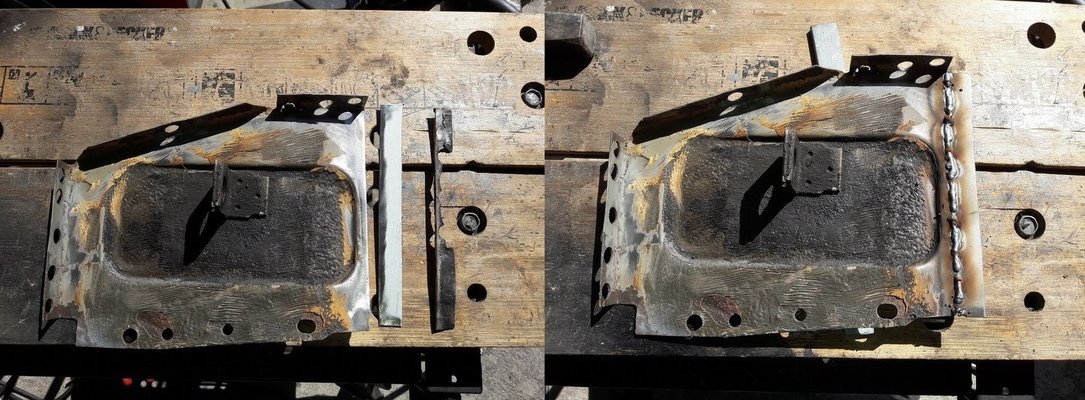
Sanding the out- and inside
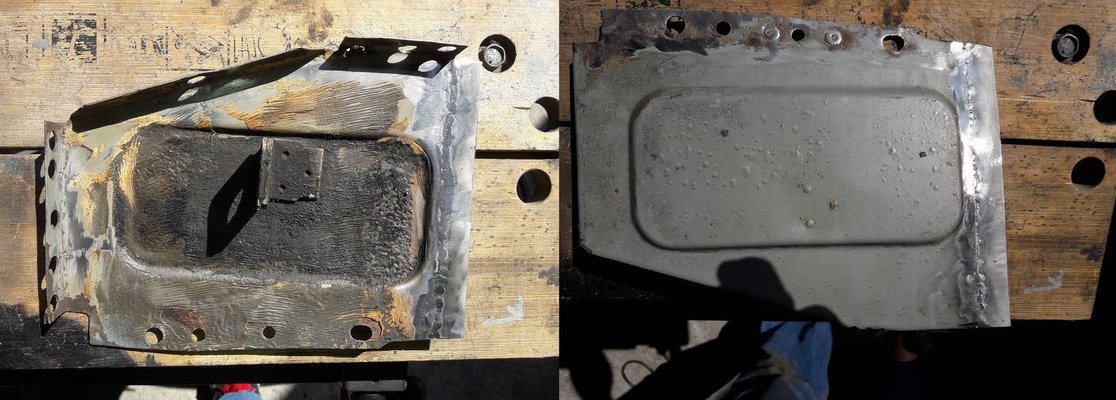
While I was doing all those things above I put my youngest son to work on rough cleaning the replacement rear axle
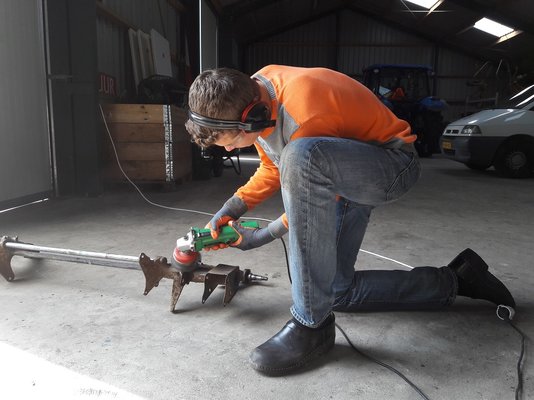
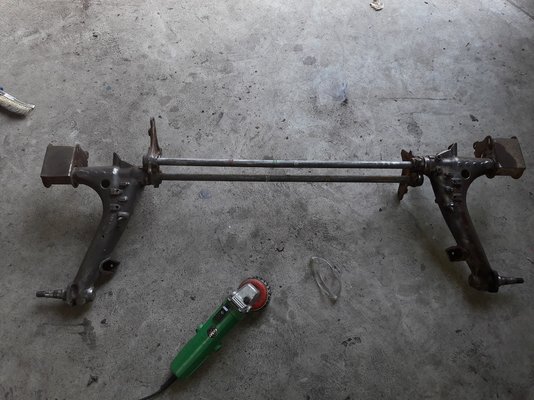
But just cleaning is a lousy job (but somebody has got to do it
) so I gave him a new challenge... (he's eager on learning new crafts and knowledge as long as it's technical). Learning how to MIG weld by himself..... (I think he peeked on his fathers Cebora welder setting's and welding art
)
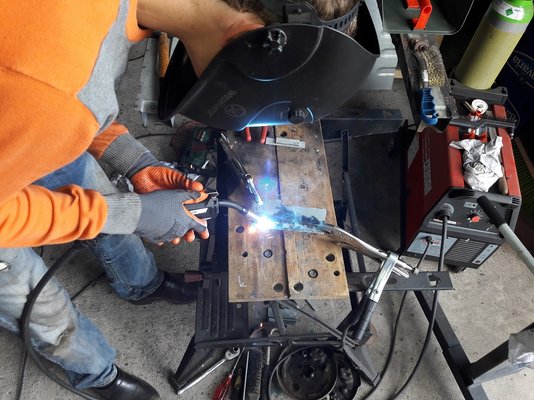
Final first results...
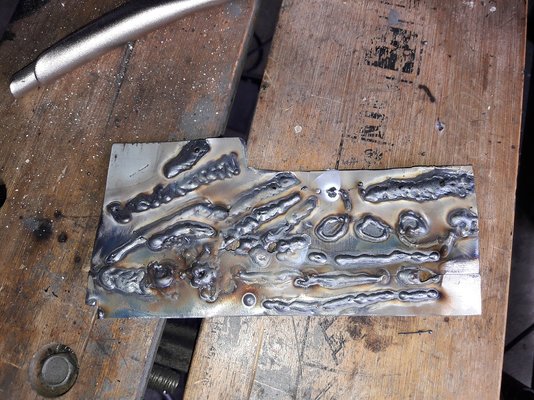
But the correct welding challenge remains for his own future safety
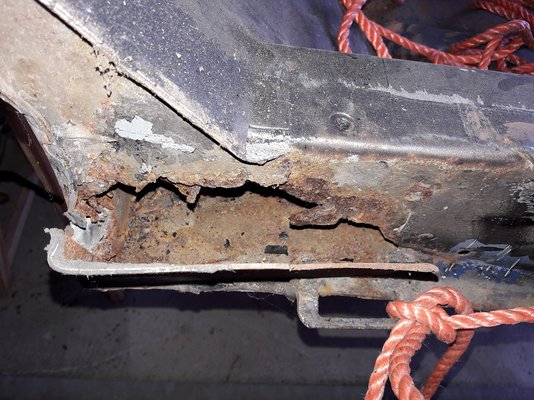
We'll keep you updated next time

New heavy metal has arrived (and still I'm a big fan of the NWOBHM as well

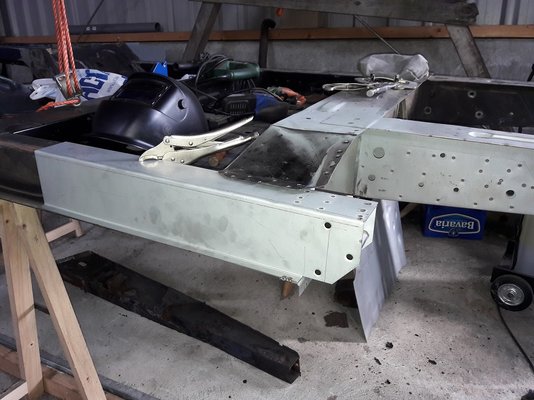
Meanwhile doing some small panel repairing...
Cutting away
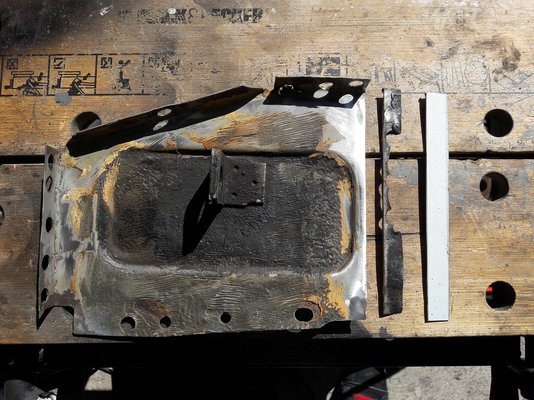
Preparing replacement steel and welding
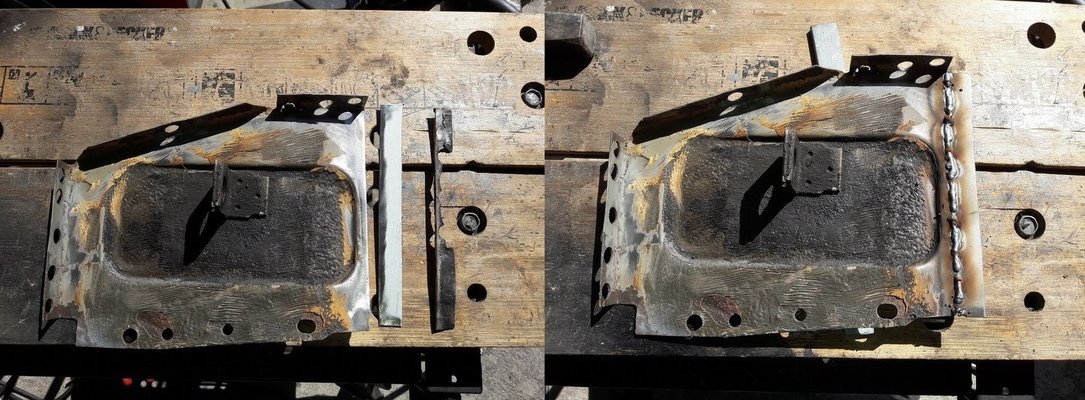
Sanding the out- and inside
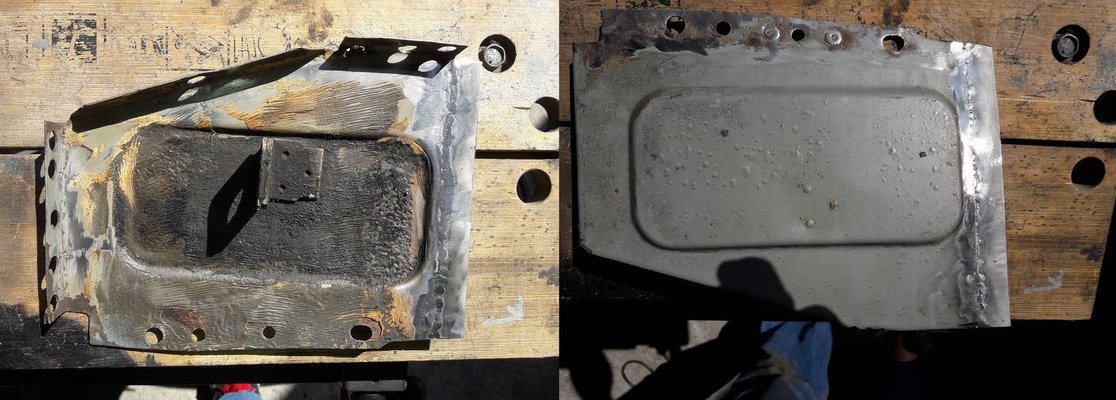
While I was doing all those things above I put my youngest son to work on rough cleaning the replacement rear axle
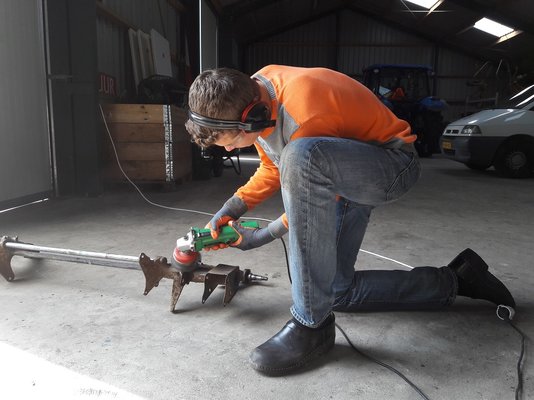
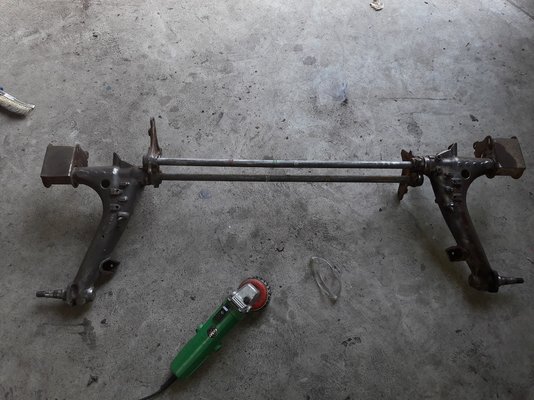
But just cleaning is a lousy job (but somebody has got to do it


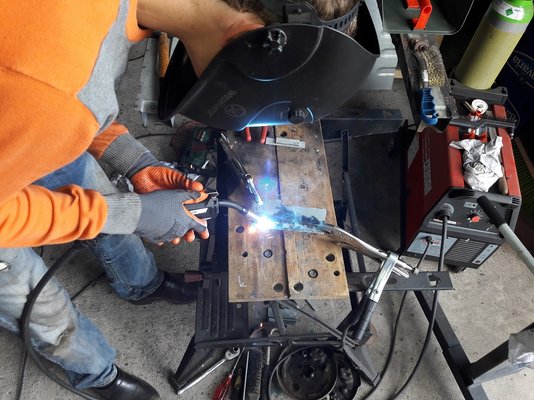
Final first results...
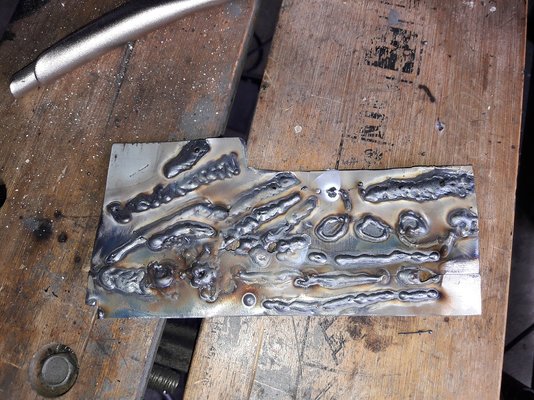
But the correct welding challenge remains for his own future safety

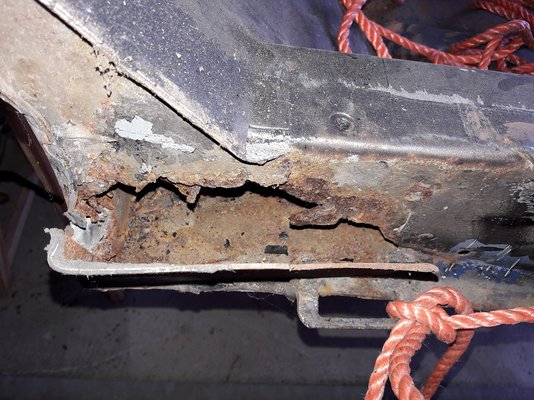
We'll keep you updated next time

Last edited: